Mga Kahanas sa Pagpili sa Mga Himan sa CNC Machining
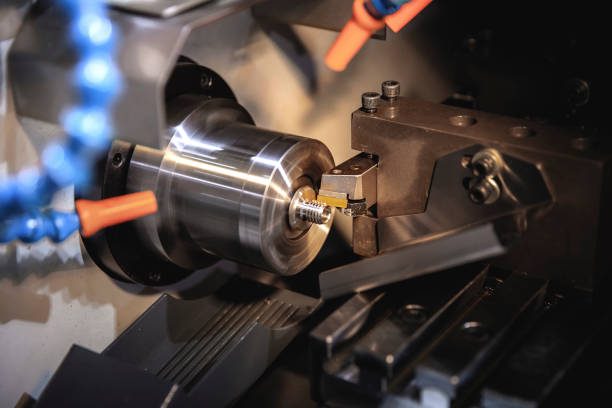
Pilia ang Tools para sa CNC Milling
Sa CNC machining, ang flat-bottomed end mill kasagarang gigamit para sa paggaling sa sulod ug gawas nga contours sa mga parte sa eroplano ug sa milling plane. Ang empirical data sa may kalabutan nga mga parameter sa himan mao ang mosunod: Una, ang radius sa milling cutter kinahanglan nga mas gamay kay sa minimum nga radius sa curvature Rmin sa sulod nga contour nawong sa bahin, kasagaran RD= (0.8-0.9) Rmin . Ang ikaduha mao ang gitas-on sa pagproseso sa bahin nga H< (1/4-1/6) RD aron maseguro nga ang kutsilyo adunay igong gahi. Ikatulo, kung ang paggaling sa ilawom sa sulud sa sulud nga adunay usa ka flat-bottomed end mill, tungod kay ang duha nga agianan sa ilawom sa groove kinahanglan nga magsapaw, ug ang radius sa ilawom nga ngilit sa himan mao ang Re = Rr, nga mao, ang diyametro mao ang d=2Re=2(Rr), sa diha nga programming Kuhaa ang himan radius ingon Re=0.95 (Rr).
Alang sa pagproseso sa pipila ka mga tulo-ka-dimensional nga mga profile ug mga contour nga adunay variable nga mga anggulo sa bevel, spherical milling cutter, ring milling cutter, drum milling cutter, tapered milling cutter ug disc milling cutter kasagarang gigamit. Sa pagkakaron, kadaghanan sa mga gamit sa makina sa CNC naggamit sa serialized ug standardized nga mga himan. Adunay nasyonal nga mga sumbanan ug serialized nga mga modelo alang sa mga naghupot sa himan ug mga ulo sa himan sama sa indexable machine-clamp external turning tools ug face turning tools. Para sa machining centers ug automatic tool changers Ang na-install nga machine tools ug tool holder kay serialized ug standardized. Pananglitan, ang standard code sa tapered shank tool system mao ang TSG-JT, ug ang standard code sa straight shank tool system mao ang DSG-JZ. Dugang pa, alang sa pinili nga himan Sa wala pa gamiton, gikinahanglan nga higpit nga sukdon ang gidak-on sa himan aron makakuha og tukma nga datos, ug ang operator mag-input niini nga mga datos ngadto sa sistema sa datos, ug makompleto ang proseso sa pagproseso pinaagi sa tawag sa programa, sa ingon pagproseso sa mga kuwalipikadong workpieces. .
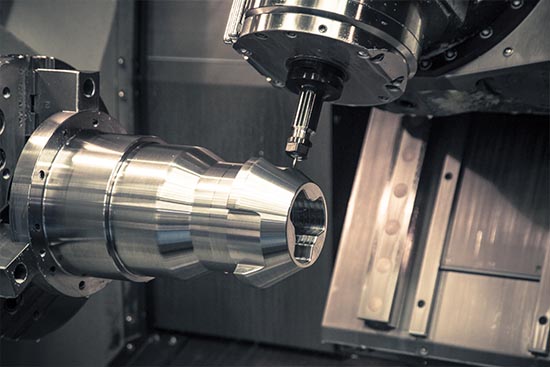
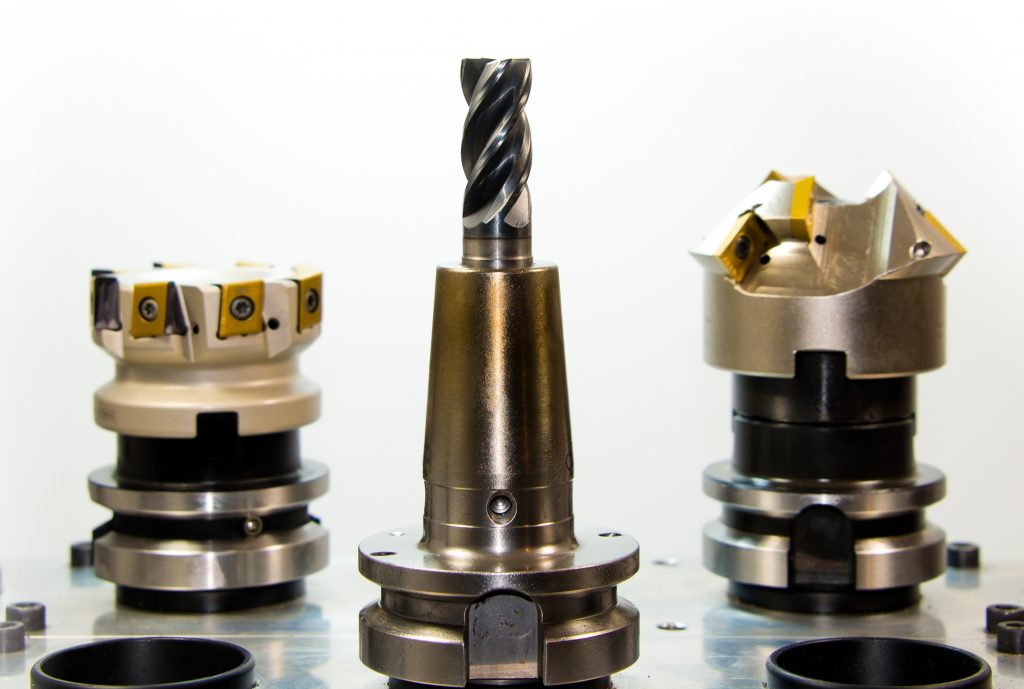
Folding Tool Point ug Tool Change Point
Gikan sa unsa nga posisyon ang himan nagsugod sa paglihok sa gitakda nga posisyon? Busa sa sinugdanan sa pagpatuman sa programa, ang posisyon diin ang himan magsugod sa paglihok sa workpiece coordinate system kinahanglan nga matino. Kini nga posisyon mao ang sinugdanan nga punto sa himan nga may kalabotan sa workpiece kung ang programa gipatuman. Busa gitawag kini nga punto sa pagsugod sa programa o punto sa pagsugod. Kini nga punto sa pagsugod kasagaran gitino pinaagi sa pagpahimutang sa himan, busa kini nga punto gitawag usab nga punto sa pagpahimutang sa himan. Sa pag-compile sa programa, ang posisyon sa tool setting point kinahanglang pilion sa husto. Ang prinsipyo sa tool setting point setting mao ang pagpadali sa numerical processing ug pagpayano sa programming.
Sayon ang pag-align ug pagsusi sa panahon sa pagproseso; gamay ra ang gipahinabo nga sayup sa pagproseso. Ang tool setting point mahimong ibutang sa machined nga bahin, sa fixture o sa machine tool. Aron mapauswag ang katukma sa pag-machining sa bahin, ang tool setting point kinahanglan nga ibutang kutob sa mahimo sa reference sa disenyo o base sa proseso sa bahin. Sa aktuwal nga operasyon sa himan sa makina, ang tool position point sa himan mahimong ibutang sa tool setting point pinaagi sa manual tool setting operation, nga mao, ang sulagma sa "tool position point" ug ang "tool setting point". Ang gitawag nga "tool location point" nagtumong sa positioning datum point sa tool, ug ang tool location point sa turning tool mao ang tool tip o ang sentro sa tool tip arc.
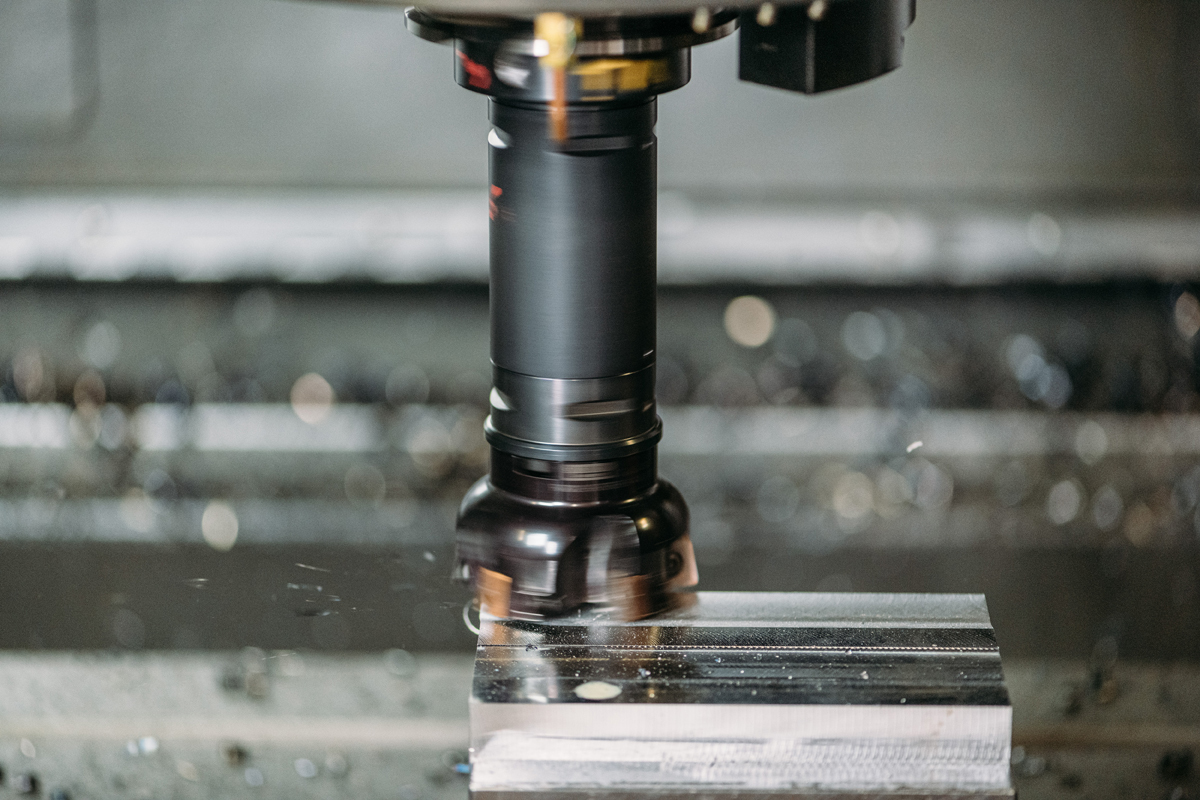
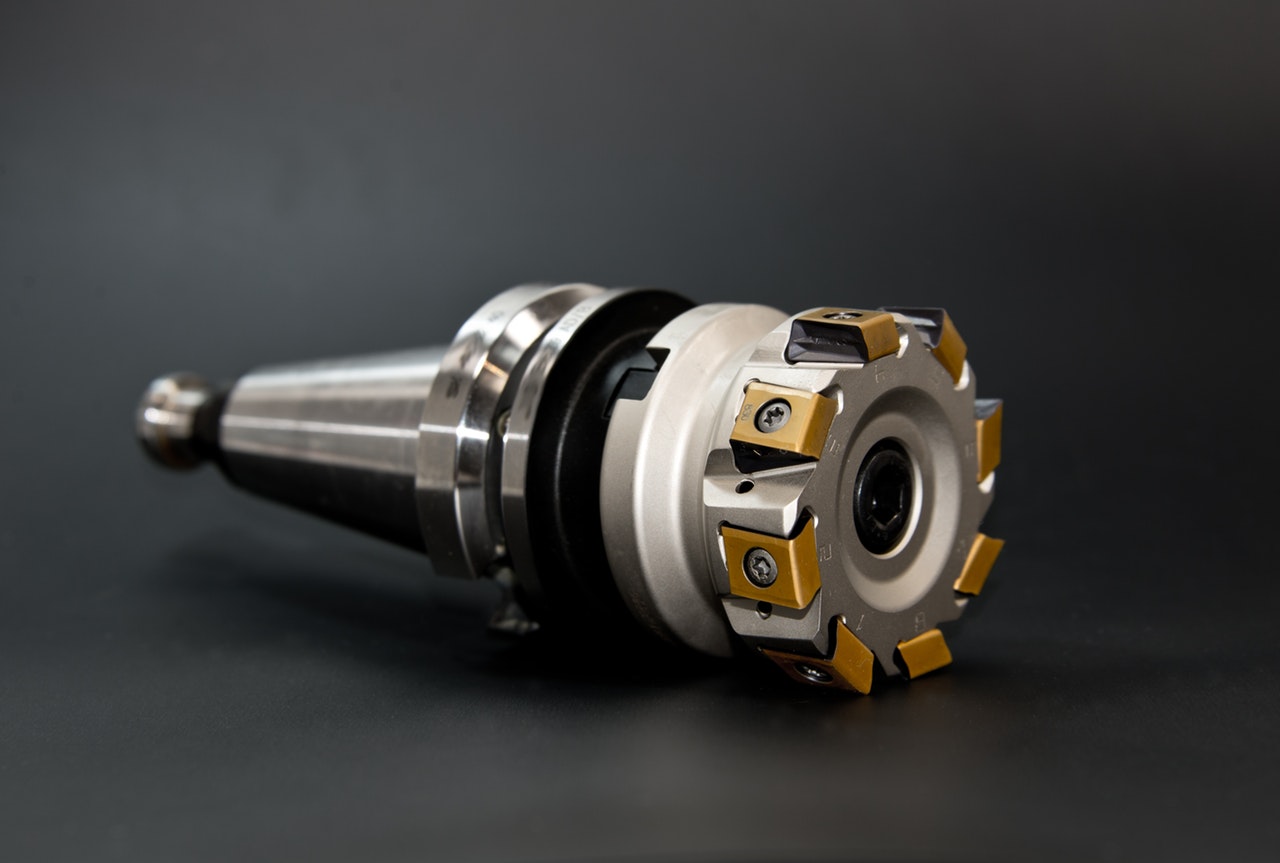
Ang flat-bottomed end mill mao ang intersection sa tool axis ug sa ubos sa himan; ang ball-end mill mao ang sentro sa bola, ug ang drill mao ang punto. Pinaagi sa paggamit sa manwal nga himan sa pag-set sa operasyon, ang pagkatukma sa pag-set sa himan gamay, ug ang kahusayan gamay. Ang ubang mga pabrika naggamit ug optical tool setting mirrors, tool setting instruments, automatic tool setting devices, ug uban pa aron makunhuran ang tool setting time ug mapalambo ang tool setting accuracy. Kung kinahanglan nga usbon ang himan sa panahon sa pagproseso, kinahanglan nga itakda ang punto sa pagbag-o sa himan. Ang gitawag nga "tool change point" nagtumong sa posisyon sa tool post kung kini magtuyok aron usbon ang himan. Ang punto sa pagbag-o sa himan kinahanglan nga nahimutang sa gawas sa workpiece o fixture, ug ang workpiece ug uban pang mga bahin kinahanglan nga dili matandog sa panahon sa pagbag-o sa himan.
Ang tumoy niini nga matang sa turning tool gilangkuban sa linear main ug secondary cutting edges, sama sa 900 internal ug external turning tools, left and right end face turning tools, grooving (cutting) turning tools, ug lain-laing mga external ug internal cutting edges nga adunay gamay nga tip chamfers. Himan sa pagliko sa lungag. Ang pamaagi sa pagpili sa geometric nga mga parameter sa gipunting nga himan sa pagliko (nag-una ang geometric nga anggulo) sa panguna parehas sa ordinaryo nga pagliko, apan ang mga kinaiya sa CNC machining (sama sa ruta sa machining, interference sa machining, ug uban pa) kinahanglan nga konsiderahon nga komprehensibo. , ug ang tip mismo sa himan kinahanglan isipon nga kusog.
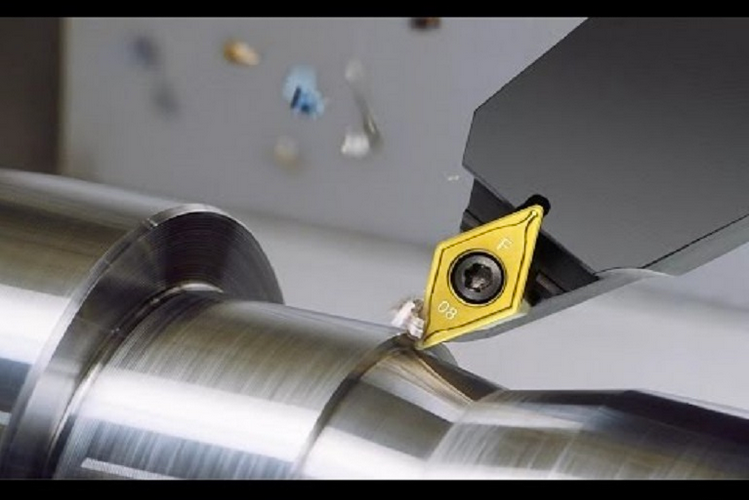
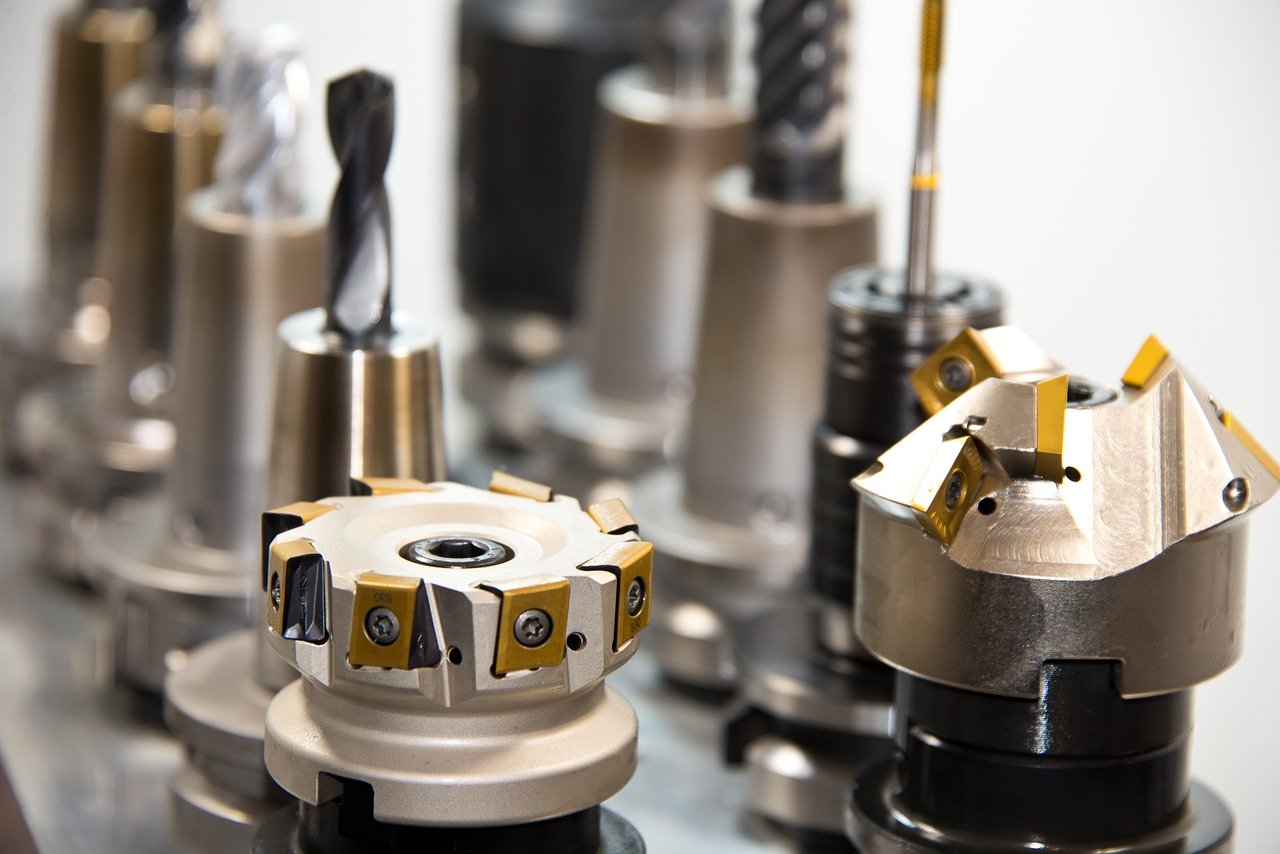
Tinoa ang Gunting nga Gidaghanon
Sa pagprograma sa NC, ang programmer kinahanglan magtino sa kantidad sa pagputol sa matag proseso ug isulat kini sa programa sa porma sa mga panudlo. Ang pagputol sa mga parametro naglakip sa spindle speed, back-cutting nga kantidad ug feed speed. Alang sa lainlaing mga pamaagi sa pagproseso, kinahanglan nga pilion ang lainlaing mga parameter sa pagputol. Ang prinsipyo sa pagpili sa kantidad sa pagputol mao ang pagsiguro sa katukma sa pag-machining ug pagkagapos sa nawong sa mga bahin, paghatag og bug-os nga dula sa pagputol sa pasundayag sa himan, pagsiguro sa makatarunganon nga kalig-on sa himan, ug paghatag og bug-os nga pagdula sa pasundayag sa himan sa makina aron mapadako ang pagka-produktibo. ug pagpakunhod sa gasto.
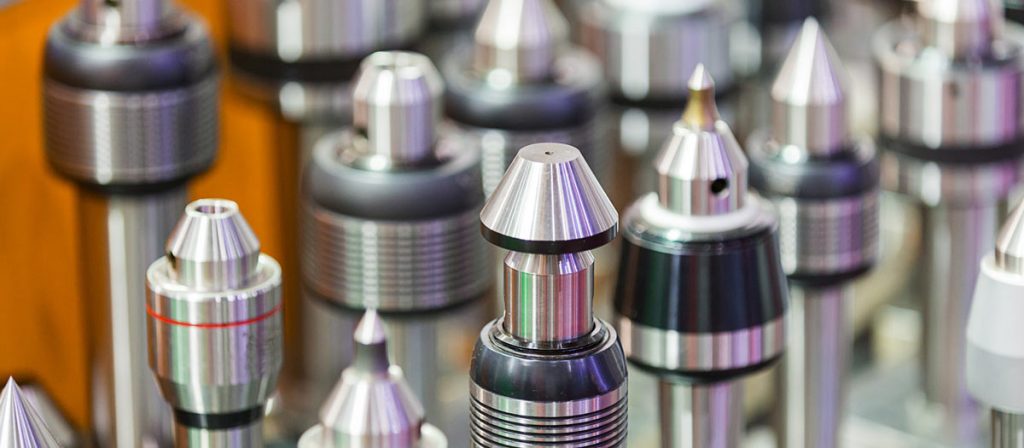